In Part 3 about mold making with hard and soft molds, Susannah Shaw shares secrets on casting foam latex and silicone.
Be sure read Part 1 and Part 2 of Model Makers The Professionals
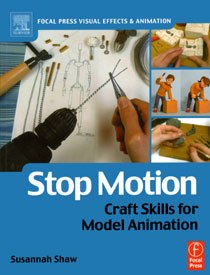
Stop Motion by Susannah Shaw. Reprinted with permission.
Casting Foam Latex
Remember to first brush your mold with a release agent (Figure 2).
The basic process for mixing foam latex is:
- foaming up to desired volume at high speed
- de-ammoniation at mid-speed * refining cell size at low speed
- gelling agent addition
You will need good ventilation when mixing latex as it gives off ammonia fumes. Depending on temperature, humidity, mixer type and size of the run, this process can take anywhere from 15 to 30 minutes. (Runs smaller than 150g of latex are not recommended.)
The following two sets of instructions are meant only as a guide and are for 150g of latex using either the Kenwood Chef mixer widely used in the U.K. (which has a choice of speeds), or the Sunbeam Mixmaster used in the U.S., (using the small bowl). The Sunbeam produces a foam of superfine mixture. It has a highly efficient beating action, driving off ammonia very quickly. However, the mixer is less efficient when used in a large bowl.
Shake all components well and into the mixing bowl, accurately weigh out: 150g latex 20-30g foaming agent 20-30g curing agent
Foaming foam at high speed for 3-5 minutes or until the desired volume is reached.
De-ammoniation reduce to medium mix speed for 3-5 mins.
Refining reduce to lowest speed for 5-6 minutes.
Gelling agent at the end of the mixing time add 5-10 ml of gelling agent to the foam. Mix thoroughly for 60-90 seconds. (The addition of a latex color at this stage will give an indication as to when the gelling agent is fully mixed in.) (The longer times given are recommended as a starting point for 300g of latex.)
Put your armature in place in your mold. The PTFE tape on your armature stops any of the brass from the armature discoloring the latex. Then fill the mold by hand, brushing the latex in to ensure coverage (see Figures 01-09).
Press together two halves and weigh them down or clamp them. Then inject the foam down one of the channels. The injection hole should direct the foam to the core. Let the foam work itself around the whole mold. When you know the latex is coming out of every vent, plug the escape vents with wet clay or English Plasticine (American clay will melt in the oven).
Sequence of photos mixing and casting with latex. Courtesy of John Parsons. Photos © Susannah Shaw.
Gelling Times
The gelling or setting time of the foam at a room temperature of 20°C (68°F) is between 10 and 20 minutes. Longer gelling times may occur and produce perfectly acceptable foams. Faster gelling times can be achieved by slightly increasing the amount of gelling agent, increasing de-ammoniation time. The foam must be set before placing in a hot oven, otherwise foam breakdown could occur. An easy way to test this is to pour leftover foam into a paper cup to a height equivalent to the thickest piece of foam you are casting. Once that has gelled, the foam in the mold should have gelled as well.
Curing
When the foam has set (i.e., become a semi-solid easily de-formed material throughout) it may be cured in a suitable oven for 2-3 hours at a temperature of 90-95°C. Curing times may vary depending on the thickness of plaster molds, etc. You may have to shorten times for fiberglass or epoxy molds, and increase curing times for thicker molds or silicone molds with plaster positives. After curing and allowing sufficient time for the molds to cool down, remove the foam from the mold and wash. Cured foam is more readily removed from warm, rather than cold molds (Figures 11 and 12).
Plaster absorbs the moisture, generally allowing air to escape, but if you find an air bubble is trapped, more likely if using a resin or a fiberglass mold, you can drill holes in the mold to allow air to escape from likely trapping places. It can take two or three bakes to get a successful cast.
Wash and trim the latex carefully with nail scissors or a scalpel (Figure 13).
Care of Latex
Latex wears well but will tear under strain. Human sweat will help to rot the latex, so keep hands as clean as possible, using wet wipes. Latex can be repaired with a contact adhesive, coat both surfaces, allow to dry and then press together.
Spirit-based cleaners will dissolve latex during the mixing and airing stages, although once baked, latex is more resistant. As with Plasticine, keep it from becoming tacky with a little talcum powder. Latex doesnt have a very long shelf life; up to six months if stored in ideal conditions. It would make sense to leave buying it until you are absolutely ready for it.
Casting Silicone
Casting silicone does not involve baking. The main consideration when using it for your puppet is that it is quite resistant (springy) and may reduce the control you have over its movements. One good solution is to cover your armature with ordinary foam upholstery foam so that you are only covering a final layer with silicone. That way you will get a reasonable response from your limbs, as well as an easily cleaned puppet.
Once youve mixed your silicone (as per manufacturers instructions), it is injected into your mold (a large syringe can be bought at a plumbers shop) until it is coming out of the vents. Remember to block any vents with wet clay or English Plasticine, as otherwise the silicone will continue to dribble out.
Leave to cure. Curing times for silicone depend on the type of silicone and how much catalyst is added. On the whole silicone will take about 10-12 hours before it can be removed from the mold.
When set, remove from the mold and clean with isopropyl alcohol. You can sand the seams with fine sandpaper, or remove them using a fine buffing tool with a Dremel or multi tool.
Coloring
For latex there are liquid latex paints that can be painted or sprayed on. Before spraying, you will want to key the cast first with liquid latex. The inks can be sponged on and thinned with white spirit. This will cause the latex to wrinkle, but it will settle again.
Water-based acrylic paint like Liquitex can give your foam latex a plasticiney look and has a good opacity and a glossy finish. Acrylics can be mixed with Copydex, or similar latex based adhesive, to bond well with the latex. For a similar look you can use a water-based gouache.
For resin or silicone pigments, check with the manufacturers for compatible dyes (Figures 14 and 15).
Costumes/Dressing
Many puppets have their clothing sculpted and molded in foam latex or silicone as part of the whole, but making fabric costumes for your puppets gives them a rich sense of individuality. The most important consideration is the scale of the fabric. You will want to look for prints and textures that suit the scale. If you want a specific pattern, you may print your own fabric.
Nigel Cornford has made costumes for puppets from the early days at Cosgrove Hall: If a fabric is too light it is liable to `crawl. In other words, youre aware of the constant movement caused by the animator touching the fabric while filming. In King Kong and the early Harryhausen movies, you can see the fur `crawling. So the material has to be stable. I start with a basic white cotton which I dye or screen print and sometimes embroider. That way you can get the scale right. I prefer not to stiffen the fabric, but if its necessary, if a cloak has to flap in the wind, Ill wire the hem or sometimes Ill stick it to Rosco foil. I prefer to hand stitch costumes for puppets, machining is not versatile enough. I would say, choose the fabric you want, and work your way around it.
If youre using leather you would want a contact adhesive. If you want a close fit, use fabric cut on the bias, that is cut diagonal to the weave of the material; you will find it gives more flexibility as you stretch it around the puppet. Remember to leave access points for any refurbishment of the puppet. It is possible to glue the fabric to a very thin layer of foam to give it maneuverability.
For decorating your fabric, pens and fabric dyes are available from craft supply shops. If you are making an additional puppet on a bigger scale, for close-ups, you will need to take the texture and pattern of your fabric into account.
During the model making process it is worth documenting and photographing each stage there is so much useful information you discover as you experiment, and it is useful to have a reference to processes used. Model making is an under-documented area combining an extraordinary range of skills and as such is always in demand for film and theatre and even medical reconstruction and prosthetics.
To read more about craft skills for model animation, check out Stop Motion by Susannah Shaw, Burlington, MA: Focal Press, 2004. 206 pages with illustrations. ISBN 0-240-51659-1 ($34.95).
Susannah Shaw is program development manager for the Animated Exeter Festival. She was head of Bristol Animation Course from 1996 to 200 at the University of the West of England and former camera assistant at Aardman (working on Close Shave among other films).